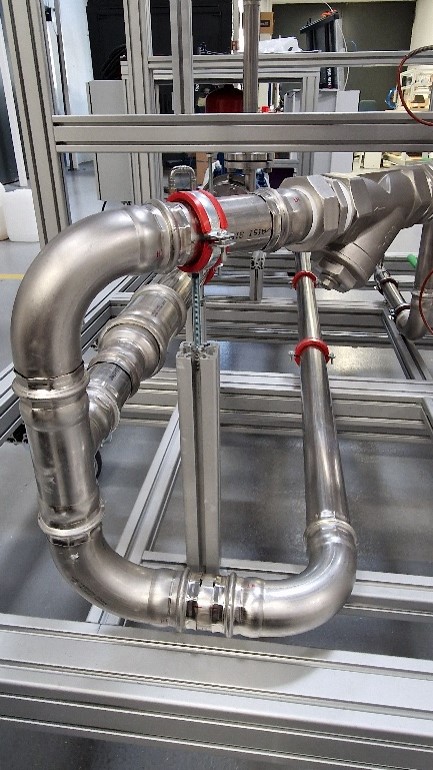
NiroSan® Industry: piping system tested with heat pumps
Freiburg: the city in the Breisgau region is not only home to the Dreisam Stadium, but also to numerous renowned research institutes, for example in the fields of energy generation, renewable energies and materials research. One of these institutes is currently conducting high-temperature tests with the NiroSan® Industry piping system.
Steam generation with large heat pumps
The tests, which are being carried out on two advanced test stands at a renowned research institute in Freiburg, are focusing on how effectively NiroSan® Industry withstands the demands of high-temperature environments – an important point for the plant operators. One aim of the tests is to generate steam using large heat pumps. These are in the 100–150 kW power range. Various steam points are tested: if superheated steam is cooled slowly, the so-called dew point is reached at some point, at which the steam is saturated again and condenses into a liquid again with further cooling. In the case of a direct transition from the gaseous to the solid state, i.e. resublimation, this point is called the frost point.
Heating thermal oil is another conceivable application. Neither of these is necessarily new – what is new, however, is the production of the pipework using a press system. It is obvious that the production of steam generators or other machines can be realised considerably faster in this way. However, pipes and fittings are not only elementary components of the system, but are also exposed to high stresses. Not every press system is therefore suitable; high-quality materials and flawless production are minimum requirements.
Heating thermal oil
One aspect of the research concerns the heating of thermal oil, where the material integrity and thermal stability of the piping system are thoroughly tested. These tests are essential for the validation of SANHA® products under realistic operating conditions. After all, operators place great value on pipes and fittings not only being functional, but also meeting the highest safety standards. These rigorous tests are intended to ensure that NiroSan® Industry can provide a reliable solution for the transport of media in such high-temperature applications.
Premium material and high-quality manufacturing
The decision to use the NiroSan® Industry piping system in both test stands – in two sizes – was made on the basis of the material, among other things. The piping system is made of the high-quality material 1.4404 (AISI 316L). This not only offers excellent corrosion resistance, but also the necessary stability and durability for demanding applications. The material contains significantly less carbon than ‘conventional’ sanitary stainless steels and, in the case of SANHA®, also at least 2.3% molybdenum. Incidentally, the entire system is manufactured in our own German plants.